Thin silicon oxide films deposited via Plasma Enhanced Chemical Vapor Deposition (PECVD) with a thickness of only few tens of nanometers already possess most of the macroscopic properties of glass, among which optical transparency, electrical insulation, chemical inertness, hardness, and low transmission against many gases, while at the same time remaining flexible and elastic.
Such films can therefore be employed as barriers for a wide array of sensitive, commercially available goods, in place of heavier, more expensive and opaque traditional materials like aluminum oxides and TetraPak-like multilayer systems.
Sensitive food products and drugs require protection against oxygen and water vapor in order to extend their shelf life. The former also need to retain their aromas inside the packaging. Bottles for sparkling drinks instead need also barriers to prevent carbon dioxide from leaving the liquid.
Electric devices like solar cells and light-emitting diodes need higher degrees of insulation against oxygen and water vapor in order to increase their life time, thus requiring multilayer encapsulations consisting of alternating barrier and buffer layers.
The deposition of both kinds of films can be easily achieved through low pressure plasma processes. The precursors are usually chosen among dozens of organosilicon compounds which are comparatively inexpensive, non-toxic, non-explosive and easily vaporized. The optimization of the other plasma parameters as well as the choice of eventual co-reagent gases allow the deposition of finely-tuned films with desired thickness, chemical composition and physical properties, equal or superior to films produced with other conventional polymerization or deposition processes.
Mariagrazia Troia M.Sc.
Ph. D. Student, Plasma Technology
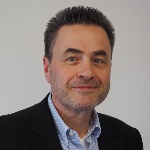
Matthias Walker
Dr.-Ing.Head of Administration / Head of Plasma Technology